Junkosha answers call to improve yields in clean environments with launch of new SLO (Super Low Outgassing) cable solution
Designed to outperform current cabling, Junkosha’s SLO solution is announced at SEMICON EUROPA 2018, Munich, in preparation for global roll out.
MUNICH, Germany. EMBARGOED: not for publication before 13 November 2018 --- In a move to help improve yields in semiconductor processing, Junkosha - the global pioneer of sophisticated fluoropolymer application technologies - has announced the development and world debut of its Super Low Outgassing cable, providing [what is believed to be] the highest performing cabling in the microprocessor clean room sectors worldwide.
Following a five-year research program, the SLO flat cable will be available through Junkosha’s team of cable experts. With the need for reduced outgassing derived from production and machine processes in the cleanroom and UHV environments increasing, microchip manufacturers are being called upon to develop more and more cleaner products for a wider set of applications. Alongside the move to a 5G world, where there will be a huge increase in the number of devices entering onto the networks, reduced outgassing throughout the chip manufacturing process will be a necessity.
According to Shinsuke Kitazawa, Junkosha’s High Flex group leader: “Our flexible SLO cable not only addresses our ambition to deliver best in market solutions, but importantly meets the demands imposed on the semiconductor manufacturing industry itself which is under constant pressure to improve yield quality and minimise any potential contamination through volatile outgassing.”
The launch of SLO is timed to coincide with SEMICON EUROPA 2018 (Munich, 13-16 November) and follows a recent call by Junkosha for the US$ 463 billion international semiconductor industry to increase collaboration on outgassing standardisation across the sector, to include the essential cabling and interconnects, integral to sophisticated microchip manufacturing processes.
According to Kitazawa, the new flexible SLO cable reaches the target vacuum level (BackGround level) in half the time compared with the conventional Low Outgas cable (ePTFE). This is an important breakthrough in the components sector, especially in the context of the International Technology Roadmap for Semiconductors, where Moore's Law can only be realised through consistent yield improvement and related productivity upgrades.
"SLO is in answer to the increasing demands of the industry. Our exhaustive tests across a comprehensive set of scenarios in vacuum chambers have demonstrated impressive results, with data providing conclusive evidence that SLO effectively outperforms its nearest competitor (ePTFE cable) by nearly two orders of magnitude in terms of release of outgassing contamination. We believe this makes SLO the clear industry leader in the specialist outgassing cable assembly market."
Growth of production in 200 and 300mm fabs is fuelled by development of the Internet of Things (IOT) and the proliferation of digitalisation will continue to increase demand for integrated circuits (ASICs), analog ICs, high-performance components and micro-electrical mechanical sensors (MEMS), all demanding efficient production processes, including the mitigation of contamination wherever possible.
Joe Rowan, President and CEO of Junkosha US and Europe explained that SLO provides Junkosha with another niche product and competitive edge. “Our focus on enabling innovation has allowed Junkosha to push the boundaries, and essentially leapfrog or outdistance competitors. This is testament to our integrated R&D, production, business development and sales teams, identifying product areas where we can excel through the application of our core, advanced PTFE Fluoropolymer technology to unmet market needs.
“By prioritising improvements in end-to-end yield, semiconductor companies can better manage cost pressures and sustain higher profitability. With the introduction of SLO to the market, Junkosha is committed to play a pivotal and leading role in the value chain of microprocessor production.”
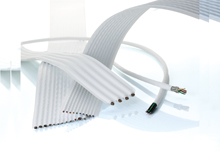
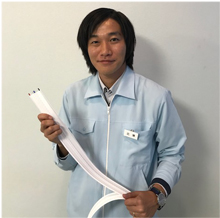