Junkosha Clear PHST Case Study – Wallaby Medical
Junkosha Clear PHST Case Study – Wallaby Medical
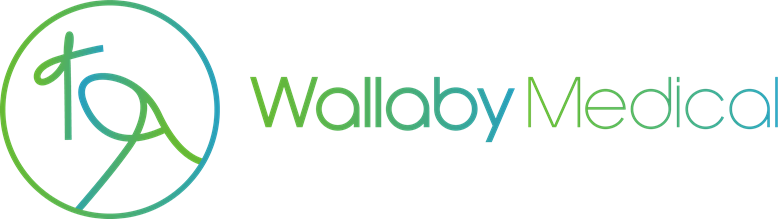
Designed to address healthcare customers’ unmet needs, Junkosha’s high shrink ratio Peelable FEP Heat Shrink Tubing (PHST) allows the use of cost-effective, lower tolerance baseline materials due to its large “take up”. This enables reflow into a single smooth construct, helping to reduce total cost of ownership for the catheter manufacturer.
Over the years, Junkosha has developed a range of new innovations, including the first ultra-small PHST and the highest-shrink ratio PHST on the market. Junkosha also provides clear PHST – designed to exhibit the same product quality as our ‘natural’ PHST but in an optically clear transparent form. With the benefit of providing visual clarity, this is a critical requirement for manufacturers not only seeking to bond, weld or tip catheters but also needing to see what is happening underneath along the underlying substrate.
Wallaby Medical is a burgeoning medical device company based in California that focuses on developing and commercializing neurovascular medical device products for treating strokes. The company uses Junkosha’s Clear PHST product for its ability to reflow the baseline materials easily into a single smooth construct, alongside the visibility it provides of the underlying materials.
The peelable design of PHST makes removing it significantly easier compared to the traditional method of skiving – saving time and reducing risk of damage to the underlying construct. For Lauren Donahue, Senior R&D Engineer at Wallaby Medical, this is a critical advantage: “The traditional process of skiving takes at least three times as long, possibly more, compared to peeling. There is also a risk of losing the entire construct from damage. Whereas skiving is a heavily operator-dependent process, peeling is very difficult to get wrong! Junkosha’s Clear PHST not only saves time but also exhibits excellent robustness and reliability”.
Using the clear format of PHST enables visual inspection of the catheter shaft both before and after reflow, enabling identification of any bubbles in the tubing and any gaps or overlap within the joints of the catheter shaft. For Wallaby Medical, this is particularly useful as its use of catheter constructs with joints in tight proximity and multiple pebax layers demands close inspection to ensure extrusions do not shift.
Here at Junkosha, we have developed a well-earned reputation for high quality, reliable consistency and excellent customer service. This was evident in our work with Wallaby Medical for whom our faster lead times were crucial in selecting a vendor to partner with. Our flexibility to work with short deadlines, without compromising product quality, is a core component of our brand values.
Looking ahead to the future, as increasingly intricate procedures become viable, the required medical device constructs will become more complicated. Device manufacturers are utilizing combinations of braiding, coils, laser cut tubing, and multiple durometer jacketing materials to increase flexibility where it’s needed, but maintain the mechanical performance necessary for a smooth delivery. With a number of PHST milestones already under our belt, Junkosha look forward to playing our part in enabling technology Innovators by leveraging our unique technologies.
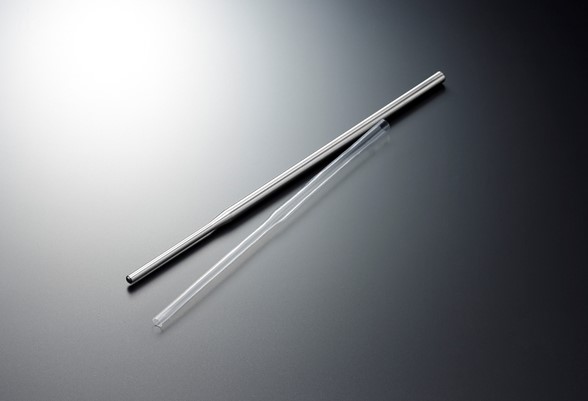